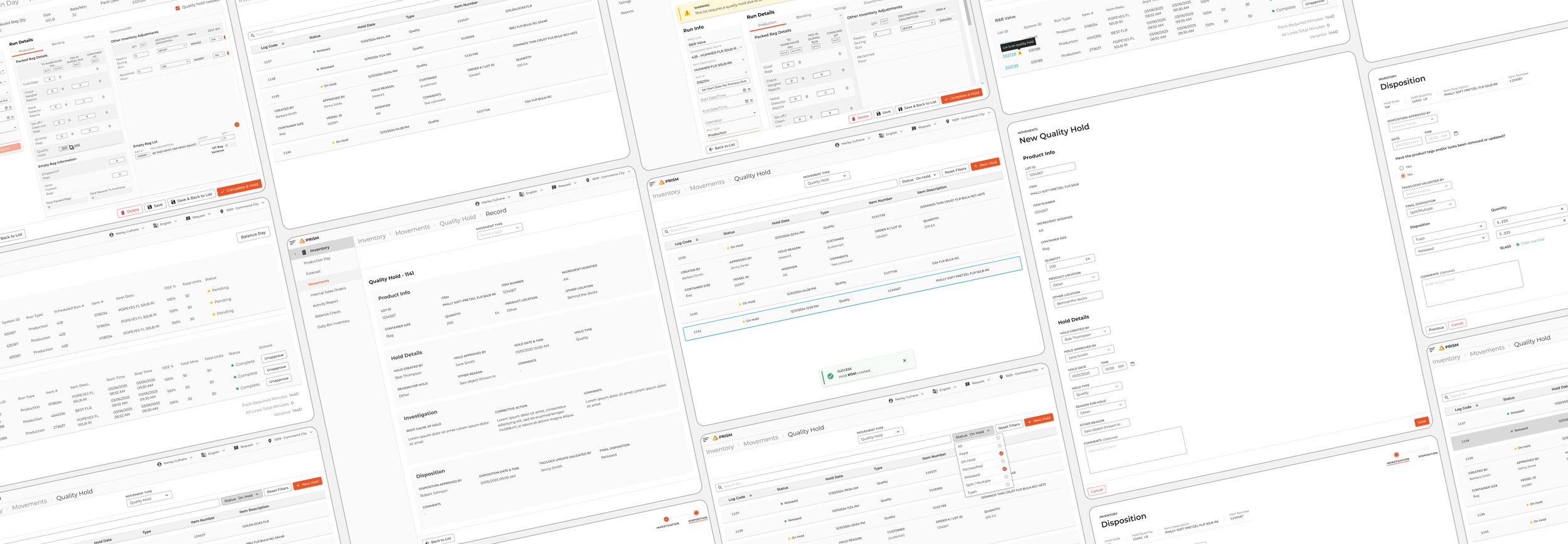
PRISM Quality Hold
Flour milling giant, Ardent Mills, blends flour to meet their customer’s functional needs. Every bag of flour has to meet the customer’s specifications as well as the company’s high quality standards. As the product designer, I led this project, finding a way to integrate the quality hold process into custom operations application.
Client
Ardent Mills
Role
Designer
Background
A manual process
In flour milling operations, maintaining quality is crucial. So, when inventory has a quality concern, like being outside of customer specifications, the inventory is placed on hold and cannot be shipped. Historically, Ardent Mills’ plants handled quality holds the old fashion way—using paper records and sticking placards on bags. The resulted was a maze of confusion and wasted time trying to hunt down inventory and figure out why it wasn’t where it belonged. Although a Power Apps tool was developed as a stopgap, it lacked integration to PRISM, the operations platform, and adoption across plants was sparse.
The Problem
No way to designate quality holds in PRISM
PRISM lacked a way to designate a quality hold, leaving the inventory on the list of shippable items. This gap left the door open for inventory in question to be accidentally shipped, risking food safety issues. To close this precarious gap, users needed a seamless way within PRISM to mark, manage, and eventually release inventory on quality hold.
The Goal
Create holds to prevent bad inventory from shipping
The goal was clear—integrate a quality hold process directly into PRISM enabling users to track inventory and ensure it could not be shipped. This initiative supported larger operational objectives to automate the inventory process, replacing paper processes with seamless digital integrations and record-keeping in PRISM.
Process
Identifying the key steps
To kick things off, I analyzed the existing Power Apps screens to get a solid understanding of the current workflow and data being captured. Couple with insights from the product manager & business users that mapped their needs, the requirements for the feature were clear. The solution needed to provide users with these key functionalities: place inventory on hold, view the hold record, and release the hold when appropriate.
Tackling challenges
The ask was essentially straightforward, even though there were quite a few pieces to it. Some details came up during later discussions that added layers of intricacy.
Multiple Integration Points: Since quality issues often surfacing during a production run, business users requested additional access to the feature directly within the production run workflow.
Mandatory holds: The design solution needed to accommodate for scenarios when the system triggered a mandatory quality hold during a production run. In these cases, the creation form needed to adapt.
The Solution
This project involved a lot of complexity and reinforced the importance of process mapping and stakeholder collaboration in designing operational tools. There were so many details, such as determining what fields were no longer relevant, identifying input selections that trigger additional fields, among other things. Through review and discussion, we made sure every aspect was covered.
Core Workflows
In total 28 screens covering 5 flows were created. The solution introduced several core flows within PRISM:
Create a Hold: Users can initiate a quality hold from various points in the workflow, including during packing or directly from inventory management screens.
Edit a Hold: Users can update hold details if circumstances change.
Repository of Hold Records: All quality holds are stored in a centralized, searchable repository for traceability and audit purposes.
Disposition a Hold: Users can release inventory from hold when quality issues are resolved. Different disposition types trigger new required fields.
View Dispositioned Records: Users can review the history and details of holds that have been resolved.
Key screens are show below:
Integration With Existing Workflows
Impact
More efficient plants, less inventory errors
Adding this feature to PRISM advances the goal of pursuing better inventory management and accuracy. In addition, it will be a step closer to reducing manual, paper-based processes in plant operations. Once it is live, it is expected to reduce headache and time wasted due to confusion over hold inventory.
Challenges
Nuanced requirements: Uncovering and planning for different scenarios for the same process.
Interdependent relationships: Designing for processes that can interact with other operational flows, requires careful coordination and validation
Lessons Learned
Identify the steps: Breaking down complex processes into clear, discrete steps simplifies the process of designing.
Understand user behavior: Insights into the business process AND how users actually behave is crucial to total understanding.
Collaboration is crucial: Ongoing collaboration with stakeholders is essential to uncover all nuances to ensure nothing is missed.